Insert Injection Molding Supplier In China
Maximize Your Savings with a Trusted Insert Injection Molding Partner
- Trusted
- Experienced
- Professional
China Plastic Insert Molding Expert
Stebro Mold is a full service custom insert molding supplier in China. We use the vertical Engel injection molding machine to produce high-quality insert-molded plastic components. You won’t have to contact multiple mold manufacturers and insert injection molding companies when you work with us. You can have the advantage of a single-source plastics provider from idea to shelf.
Our services include:
- 2D & 3D product design and optimization
- The material selection
- Rapid prototyping services
- Cost-effective insert mold solution
- Mold Flow Analysis to optimize the mold design
- In-house insert mold manufacturing, mold change, mold trial, tooling transfer and maintenance
- Pre-production runs and mass production
Part Assembly
We’re here to make sure your projects are a success! With our help, you’ll get insert molded parts done correctly from the start, within your budget, and on time.
insertmolding examplesI
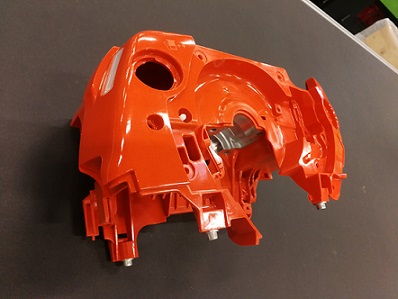
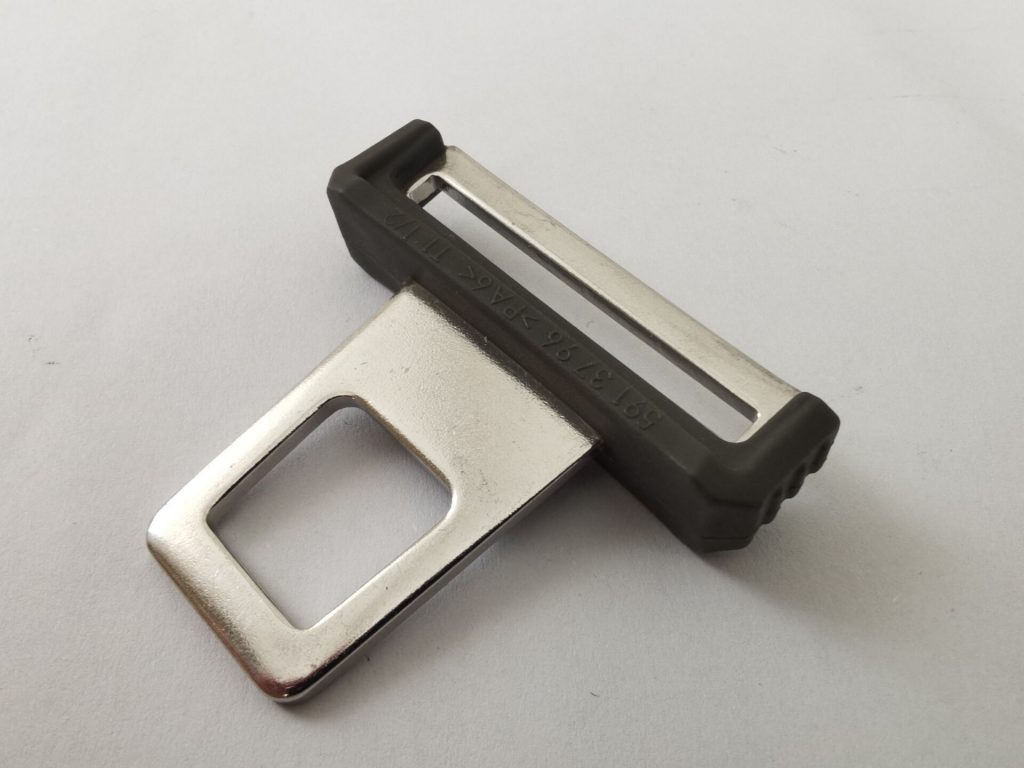
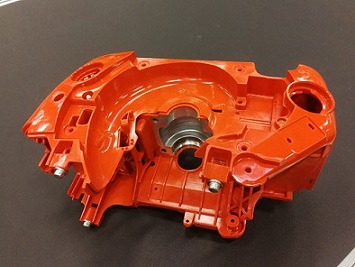
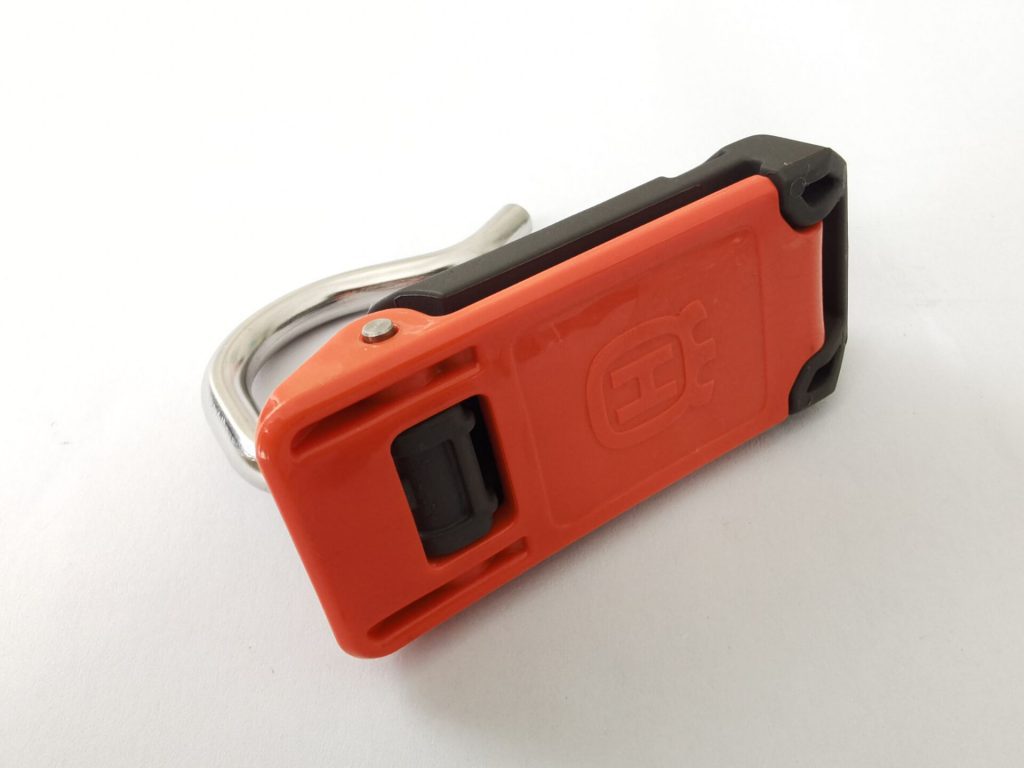
Why Stebro Mold for Insert injection Molding Supplier
- Free Insert Molded Plastic Part Design Assistance
- Mold design optimize with Moldflow to improve the surface and reduce cost
- In-house Insert Mold Manufacturing
- Procurement or manufacture of metal inserts
- Mold Life Guarantee, Free Mold Maintenance
- Affordable Price, No Hidden Charges
- Quality Control In Manufacturing, Consistent Quality
- On Time Delivery
- 24-Hour Quote Responses With DFM Feedback
- Engel Vertical Injection Molding Machine
Customer Letters
What is Insert Moulding?
Insert molding is an injection molding manufacturing methods in which pre-manufactured inserts, such as metal or other components, are placed into a mold tool first, then inject molten thermoplastic resin around the inserts to form a single, integrated part. It can reduce assembly time and cost, as well as improve the strength and functionality of the final product.
Insert Injection Molding Process
- Preparing the inserts: The metal inserts are cleaned and prepared for integration with the plastic material. Depending on the application, surface treatments or coatings may be applied to improve adhesion.
- Mold setup: Ensure that the mold is clean and free of any debris or contaminants.Install the insert mold into the injection molding machine and verify that it is properly aligned and secured. Configure the machine settings, such as temperature, pressure, and injection speed, according to the requirements of the specific plastic material and insert being used.
- Positioning the inserts: Manually or automatically place the prepared inserts into the designated areas within the mold cavity. Ensure that the inserts are accurately positioned and secured to prevent movement during the molding process.
- Injecting the plastic: Inject the molten plastic resin into the mold cavity, ensuring that it flows around and completely encapsulates the inserts.
- Cooling and solidification: The plastic cools and solidifies around the insert, creating a strong bond between the materials.
- Ejection: Once the plastic material has fully solidified, carefully open the mold to release the part. Utilize an ejection system, such as ejector pins or a stripper plate, to ensure smooth part removal without damaging the plastic or dislodging the inserts.
- Inspect the finished parts for quality and consistency: Examine each part to ensure proper insert placement, bonding, and overall part quality. Perform any necessary quality control tests or measurements to verify that the parts meet the required specifications.
- Post-Processing (if necessary): Trim any excess plastic material such as sprue remnants from the parts. Conduct any necessary secondary operations, such as painting, surface finishing, or assembly, depending on the specific application requirements.
Insert Moulding Advantages
- Improved precision
- Increased design flexibility
- Reduced assembly and labor cost
- Enhanced functionality
- Improved strength and durability
Insert Moulding Disadvantages
- Complex process
- Limited material options
- Challenges with insert placement
- Increased risk of defects
- Higher tooling cost
Insert Molding Application
Insert molding process is a manufacturing process that combines multiple materials into one injection molded part. It results in a stronger, more durable, and functional product with reduced assembly time and cost, improved precision, and increased design flexibility. It can be found in wide range of industries including Automotive, Electrical and Electronics, Medical Devices, Consumer Goods, Aerospace, and Industrial Equipment.
Insert molding design guide
Main considerations in designing insert molding product
- Evaluating Material Bonding and Adhesion such as abrasion resistance and pull out resistance.
- Plastic components and metal inserts are designed for mechanical bonding
Key considerations in Insert Mold Design guidelines
- Material selection for both the insert and plastic
- Shrinkage factor for the plastic materials
- Geometry for both the plastic and insert such as wall thickness
- Putting the inserts into the mold by robot or manual
- Insert placement and retention in the mold
- Feeding, Cooling, Ejection, and venting system in the mold
Insert Injection Molding Cost
Insert plastic component cost=molding materials cost + insert costs + injection molding cost
There are some ways to lower the cost:
- Reduce the material cost
- Optimize the mold design to shorten the molding cycle times
- Increase the cavity number in the mold.
- Working with a full-service insert injection molding company
Insert Molding Machine
- Horizontal Molding Machine
- Vertical Molding Machine
Insert Molding Inserts
- Brass, blinded threaded, threaded steel parts, threaded inserts for plastic molding
- Steel, stainless steel, screw machine parts, CNC machining parts, metal stamping parts for injection molding inserts
- Photochemical etched parts, cold-headed parts, die-casting part
- Insulated wires, flexible circuits, lead frames, ceramic, and composite insulators
Lorem ipsum dolor sit amet, consectetur adipiscing elit. Ut elit tellus, luctus nec ullamcorper mattis, pulvinar dapibus leo.