Ultem Injection Molding & PEI Injection Molding Supplier In China
Maximize Your Savings with a Trusted Custom PEI Injection Molding Manufacturer in China
- Trusted
- Experienced
- Professional
PEI Injection Molding Services
Stebro Mold specializes in delivering high-quality, custom PEI injection molded products for a wide range of industries, including aerospace, automotive, medical, and electronics. we provide end-to-end PEI injection molding solutions, from design to delivery.
Our services include:
- PEI product design and optimization
- ULTEM PEI plastic resins selection
- Rapid prototyping services
- In-House injection mold tool manufacturing, tooling transfer, mold change, and maintenance
- PEI injection mold trial
- Pre-production runs and mass production
- Secondary services include surface finishing, assembly, and packaging to deliver a complete, ready-to-use product.
When you choose Stebro Mold, you get more than high-quality PEI injection molded parts. You also gain a team of experts dedicated to helping you succeed in the long term. Let us help you bring your vision to life with our unparalleled services and support.
Why Stebro Mold for Ultem Molding
- Free Product Development & Part Design Consultation, Moldflow Analysis
- Mold Life Guarantee, Free Mold Maintenance
- Affordable Price, No Hidden Charges
- Quality Control In Manufacturing Process, Consistent Quality
- On Time Delivery
- 24-Hour Quote Responses With DFM Feedback
- Engel Injection Molding Machine
PEI resin
PEI resins are a family of high-performance polymers. It is known for their exceptional properties, such as high temperature resistance, mechanical strength, and dimensional stability. One of the most prominent members of this family is ULTEM™, a trademarked pei resin produced by SABIC. Ultem 9085, Ultem 2300, and Ultem 1000 have become popular choices for high-performance polymers across various industries.
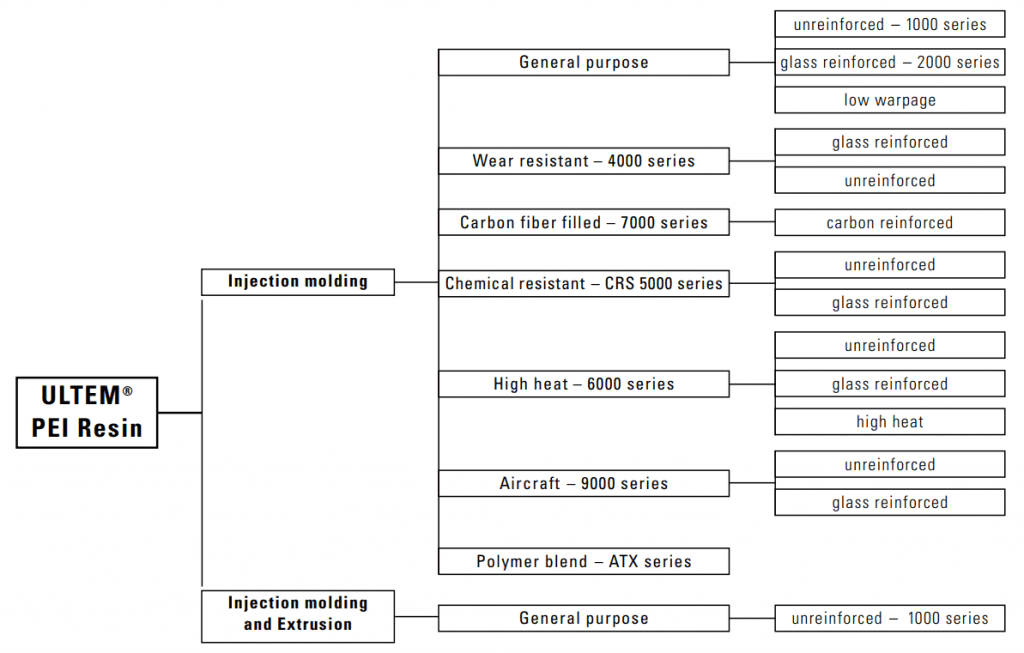
PEI Molded Components Application
Ultem 9085 has a high Limiting Oxygen Index (LOI) and low NBS smoke evolution. Ultem 1000 has exceptional flame resistance. Due to its remarkable properties, it has found widespread use across various industries.
1, Aerospace:
- Interior/exterior components
- Electrical parts
2, Automotive:
- Under-the-hood parts
- Exterior/interior components
3, Medical Devices Industry:
- Surgical instruments
- Diagnostic equipment
- Implantable devices
4, Electronics:
- Electrical insulation
- Consumer electronics
5, Oil and Gas:
- Exploration equipment
- Downhole components
- Pipeline infrastructure
6, Food and Beverage:
- Food processing equipment
- Food storage containers
- Microwave cookware
PEI Material properties
- Elevated temperatures resistance up to 340°F (170°C)
- Remarkable high strength and rigidity
- Superior dimensional stability
- Excellent chemical resistance
- Impressive electrical properties
- Inherent flame retardancy (UL94 V-0)
- Optimal optical properties, including UV resistance
- Strong environmental resistance
China PEI injection molding cost
There are lots of PEI plastic injection molding manufacturers in China. Some of them have PEI medical grade injection molding classrooms. Custom PEI molded parts cost can fluctuate due to factors like material cost, mold production, cycle times, production volume, and additional operations. Reach out to a Chinese PEI injection molding supplier for an accurate quote tailored to your project’s unique needs.
Ultem Processing Guide
Part Design - Design for Manufacturing
- Plastic Material Selection: Choose the appropriate PEI resin based on the application requirements.
- Wall Thickness: Ensure consistent wall thickness throughout the part to prevent sink marks, warping, or dimensional issues. Aim for a PEI part wall thickness between 1 to 4 mm, depending on the application.
- Draft Angles: Add draft angles in the design for easier part ejection from the mold. Apply a minimum draft angle of 1-2 degrees per side, with larger angles for more complex geometries.
- Ribs and gussets: Add ribs and gussets to increase structural support without thickening the walls. Design ribs with a 2:1 to 3:1 height-to-thickness ratio and about 50-60% thickness of the adjacent wall.
- Radii and fillets: Use radii and fillets at corners and intersections to enhance material flow, reduce stress, and improve strength. Design radii to be at least 0.5 times the adjacent wall thickness for optimal structural integrity.
- Bosses: Add bosses in the design to accommodate screws, inserts, or other fasteners.
PEI Mold Design
- Mold steel: Select a suitable mold material, such as S7 or H13, to withstand the high processing temperatures required for PEI.
- PEI Shrinkage: The typical shrinkage rate is around 0.5 to 0.7%.
- Gate and Runner System: Common gate types for PEI parts include edge gates, submarine gates, and fan gates. Work with the injection molding manufacturer to determine the most appropriate gate type and location. It can optimize material flow and minimal part defects.
- Cooling System: Implement an efficient cooling system within the mold to ensure uniform cooling and minimize cycle times. Proper cooling helps to reduce part warping, shrinkage, and other defects associated with uneven temperature distribution.
- Venting: Include sufficient mold venting to avoid trapped air or gas causing short shots or burn marks. Position vents where material flow fronts converge and ensure proper size and placement for air escape without material leakage.
- Ejection system: Create a sturdy ejection system for easy, damage-free extraction of the finished part from the mold. Consider using ejector pins, sleeves, or stripper plates, and ensure they are strategically positioned to avoid part deformation or damage.
- Mold Surface Finish: Choose an appropriate mold surface finish based on the desired appearance and functionality of the final part.
- Mold Maintenance: Design molds for easy maintainance.
Injection Molding Parameters
- Drying Material: Dry PEI resin at 150°C for 4-6 hours before processing. This is to eliminate residual moisture and avoid hydrolysis or splay issues.
- PEI Mold Temperature: Incorporate an efficient temperature control system within the mold to maintain consistent temperatures. The temperature should generally range from 225°F to 350°F (107°C to 177°C).
- Melt Temperature: Set the barrel temperature profile for PEI between 640°F and 750°F (338°C to 399°C). This will ensure a uniform melt and minimize degradation.
- Screw Speed: Adjust screw speeds to allow continuous rotation throughout the cooling cycle without extending the overall cycle time.
- Back Pressure: Set back pressure at 50-100 psi (0.35-0.7 MPa) for a uniform melt. Avoid high back pressure to prevent degradation and splay. Use low back pressure for reinforced grades to protect glass fibers. Minimize decompression and suckback to maintain part surface quality.
- Shot Size: Aim for a shot size between 30% and 80% of capacity. For color-critical blended grades, target 80% barrel capacity to minimize residence times.
- RAM Speed: Utilize fast fill for better flow and finish. Use slow fill for sprue/edge-gated parts, thick components, and small-gated pieces. Begin with slow injection to avoid issues.
- Injection Pressure: Injection pressure depends on factors like melt temperature, mold temperature, part geometry, and equipment considerations. Choose the lowest pressure that achieves desired properties, appearance, and molding cycle.
- Cushion: Employ a nominal cushion (1/8 inch recommended) to decrease barrel residence time and account for machine variations.
- Cycle Time: Adjust the cycle using fast injection speed, minimum holding time for gate freeze-off, and short cooling time. ULTEM® resin often reduces cycle time compared to other thermoplastics and thermosets. Part thickness is the key factor affecting cycle time.
By following best practices and design guidelines, you can improve the thermoplastic injection molding process. This will help you create high-quality, reliable PEI plastic parts that meet your project needs. Stebro Mold has rich experience in Ultem 2300 injection molding, Ultem 9085 injection molding and ultem 1000 injection molding.
Contact us today to discuss your PEI molded parts manufacturing needs. See how we can help you succeed with Polyetherimide molded parts manufacturing.